Ceramic metallization is critical in making strong and dependable joints between ceramic and metal parts, which ensures the smooth functioning of many sophisticated applications. This process consists of plating a metal layer on the ceramic surface in order to assist in joining ceramics with metals, typically through brazing. Its integration in industries such as power electronics packaging and sensor technology is urgent because ceramic metallization makes it possible to utilize the high thermal stability, hardness, and other excellent properties of ceramics along with the conductivity and mechanical strength of metals.
Technology Characteristics Introduction
Our ceramic metallization solutions utilize both thick and thin film technologies, offering flexibility for a variety of applications. By applying proprietary inks and coatings tailored to individual customer requirements, we help create robust, long-lasting ceramic-metal assemblies. Whether the goal is to form an electronic circuit path or to join a metal component with ceramic, we guide our customers in selecting the most effective and cost-efficient materials and bonding methods. Ceramic brazing suppliers often turn to our solutions for their reliability and precision.
One of the most advanced techniques we offer involves the use of refractory metallized coatings. This process applies molybdenum-based paints, followed by nickel plating, to form an interface that enables ceramic and metal to be joined via brazing, resulting in hermetically sealed joints. After sintering, a layer of molybdenum-manganese, typically 10 to 50 µm thick, is deposited, ensuring a strong bond between the metallized layer and the ceramic base.
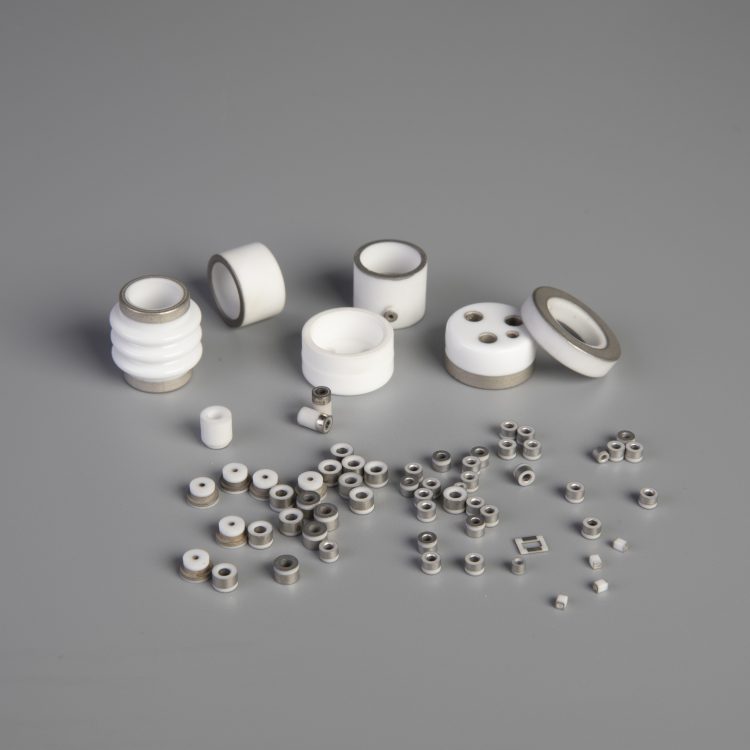
metallization ceramic filament supports
Product Introduction
Our metallization methods include various deposition techniques to suit different component geometries. For cylindrical ceramics, we use a proprietary automated deposition method that ensures consistent uniformity of bandwidth and coating thickness. For other forms, screen printing, pad printing, and brush coating are employed to apply a thin nickel layer, usually 2-10 µm, on the molybdenum-manganese layer, creating the required wettability for subsequent brazing.
In addition to refractory metallized coatings, we offer thick film deposition using precious metal pastes such as gold, silver, and copper. These pastes are fired onto the ceramic at 850°C, forming a secure interface that can be applied in multiple layers for increased coating thickness. This technology is perfect for applications like instrumentation, control systems, guidance systems, IR and UV detectors, and circuit boards.
For situations requiring thin metallized layers, we offer options such as aluminum, gold, and titanium coatings. These coatings are typically 1-2 microns thick and can be applied in virtually any pattern. Multi-layer coatings, such as nickel-chrome or nickel-gold, can also be applied, with the possibility of electroplating afterward for added functionality.
Product Advantages
We’re impressed by industry leaders’ choices of source to obtain aim engineering’s services/features. Some of the leaders join us discussing how our competitors have invested heavily in ceramic metallization engineering services at the expense of their metal-to-ceramic seal suppliers claim to fame. But there is no competition strive out of them. Their ropes-long outperforming aim engineering. As industry insiders precious clay and precious metal find its application in ceramic metallurgy. Turns out almost every ceramic can be modified in a unique way to serve a specific purpose.
Application Scenarios
Ceramic metallization is needed in power electronic packaging since effective heat and electrical conduction requires robust and dependable joining of metal to ceramic components. Other applications are seen in sensors, instrumentation, and control systems that require joining of ceramics to metal for effective performance. Our solutions are useful in various industries, especially in aerospace, automotive, medical, and industrial manufacturing where high quality bonds are demanded by sophisticated technologies.
At InSealing, we strive to develop ceramic metallization solutions that distinctly serve the requirements of our clients. Please do not hesitate to contact us if you need information about our products and services and how they can be of use to you.